DIGITAL TWIN BUILT ENVIRONMENT
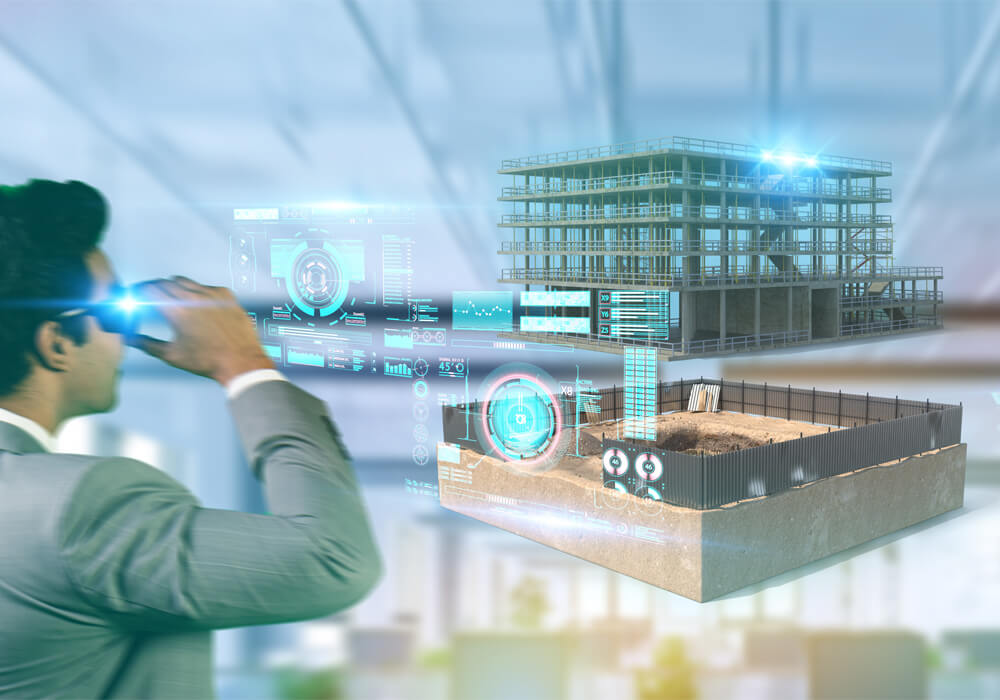
Digital Twin
A Digital Twin (DT) is “a virtual model designed to accurately reflect a physical object.” Although this description seems very close to BIM, it actually represents a natural and consequent extension of it. In the case of the DTs, the digital model of the work does not only want to faithfully represent its real twin in terms of geometries, information and characteristics, but to establish a link between the two through further enabling technologies. At more advanced levels, a DT could add real-time data from a currently deployed situation to be able to look at real-time scenario planning. This allows you to optimize the use of the asset by realizing significant savings in maintenance and adapting to the actual use of the building.
Dynamic and hybrid informative infrastructure
To create this dynamic and hybrid information infrastructure, a network of sensors carefully designed to reflect the physical behavior of the work in the DT cannot be ignored. Building Information Modeling (BIM) is a process that allows you to create a multidimensional digital model of an entire asset that takes shape even before construction and then evolves with the work during the construction and operating phases, becoming its “digital twin”. In a virtual environment, the function of the “digital twin” is to contain all the information that take part during the life cycle of a work and acts as a system for identifying any actions to be performed to maintain the integrity of the infrastructure. Predictive maintenance is the primary use case for the application of digital twins in Industry 4.0.
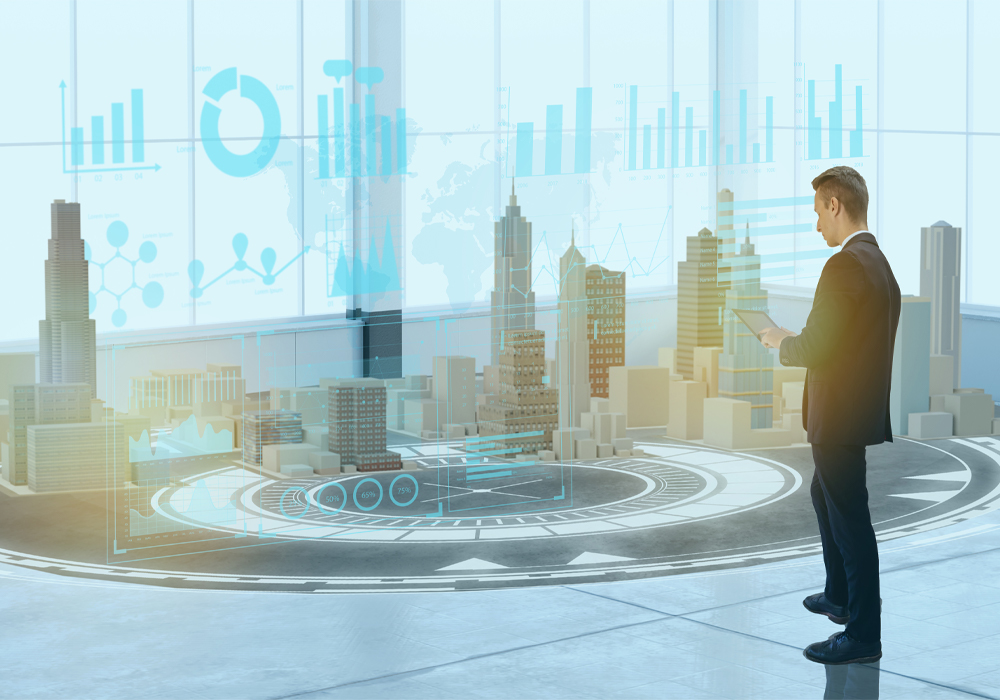
Intelligent Management Approach
The approach is also widely used in smart facility management, where advanced predictive practices are estimated to generate up to a 20% reduction in a building’s maintenance and energy costs. IoT and Digital Twin technologies with smart facility solutions are fundamental for generating these savings, because they enable maintenance needs to be accurately determined before failure or downtime occurs. Sensors, BIM and other enabling technologies actually allow P.B.S.M. to provide services for the development of intelligent buildings and Smart Maintenance. Buildings can now be made to sense and communicate their exact state in order to allow the analysis of what is happening inside, simply by interrogating their DT. For example, it is possible to set the temperature throughout the building, minimizing the energy use in unoccupied areas, to keep structural stress levels under control and to adjust lighting on demand. Furthermore, DT is characterized, like BIM, by a strong modularity and scalability. In fact, it is possible to choose to collect information only on characteristics that have value, such as the number of people in a specific area of the building, the usury of some elements of the system or the opening status of the windows on a specific side. There is no need to digitally map and track the entire asset.